Influence of electrolytes on liquid-liquid equilibria for extraction processes
Volltext
Abbildung
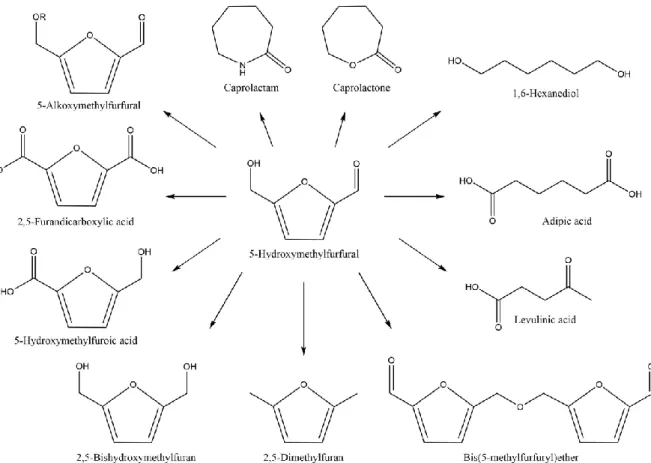

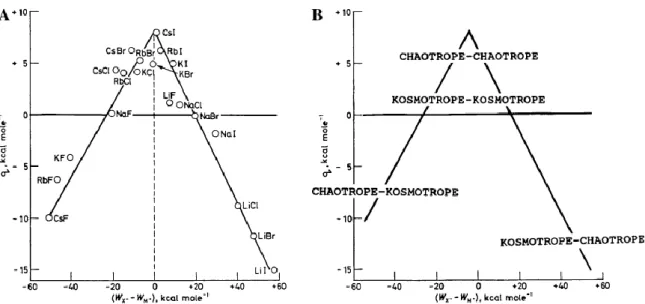
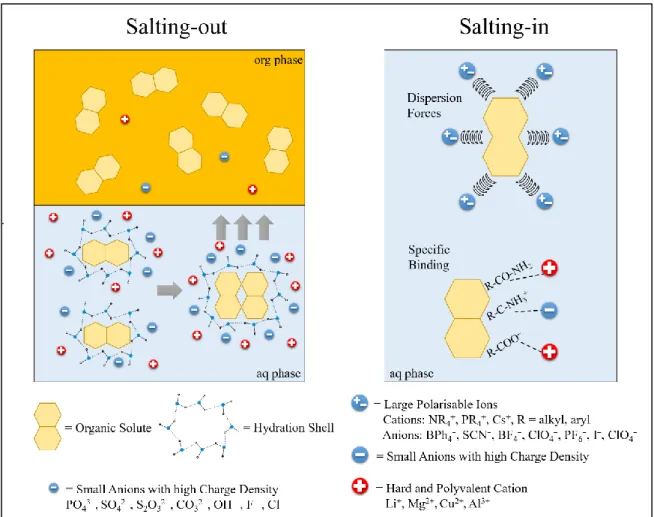
ÄHNLICHE DOKUMENTE
It was shown that complexes of Ti(III) and Co(II) appeared in the melt due to the reaction 2Ti(IV) + Co → 2Ti(III) + Co(II) and this reaction was entirely shifted to the right
The standard rate constants for the redox reaction Eu(III) + e , Eu(II) were calculated from cyclic voltammetry dataE. The sluggish kinetics of this reaction is discussed in terms
A refinement of the model based on liquid-liquid equilibrium data can lead to quantitative improvements of the predictive quality for these complex
For the assessment of water treatment processes, the changes of all detectable compounds were regarded based on the detected signal heights in the influent and
In the ternary system Re/Mo/O four series of mixed oxides have been prepared by heating of powder samples and by transport reactions. Contributions to the understanding of the
This work also investigated the influence of the Sherwood number on the computed concentrations of different species, it is shown that any value of the Sherwood number used within
The long-lived species exist in both the plasma and air-gap regions, and are absorbed into the liquid phase.. The aqueous species exist in the liquid phase and can be desorbed
The temperature dependence of the velocity from the present and recently reported [5] hypersonic data are summarized in Table 2 together with ultrasonic data [4]. All the