Novel bio-based materials from cellulose and chitin
Volltext
Abbildung
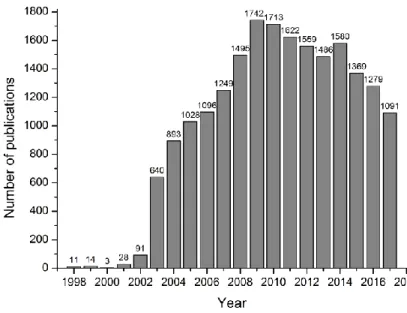
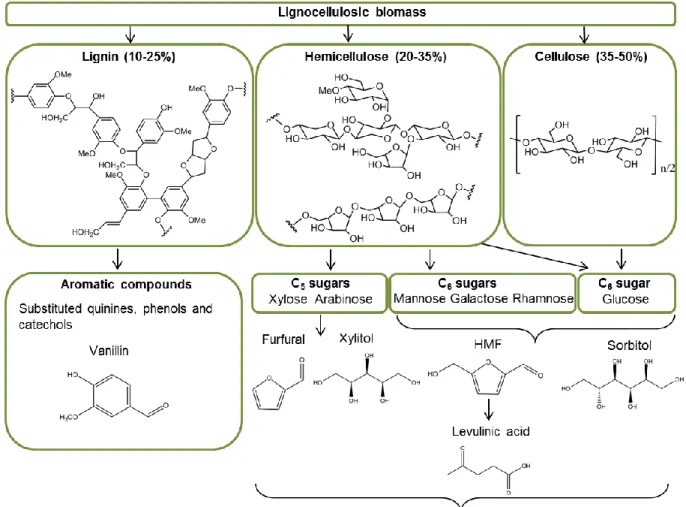
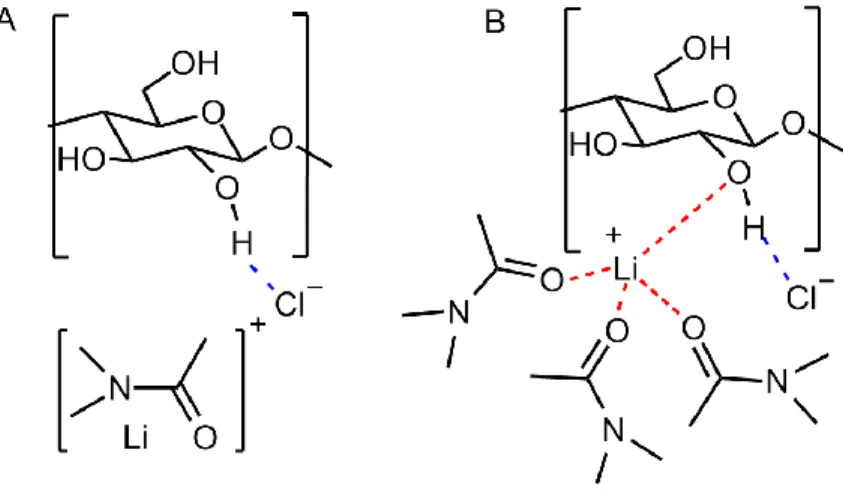
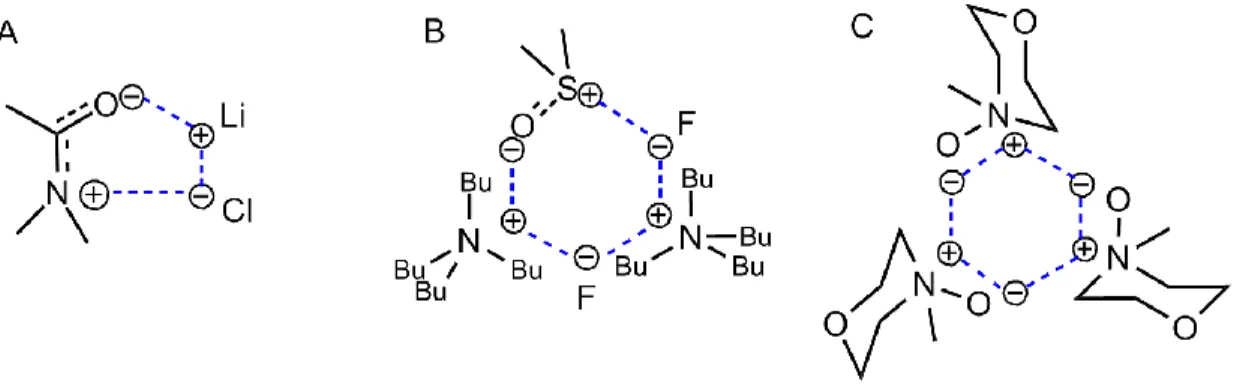
ÄHNLICHE DOKUMENTE
The aim was to identify patterns regarding the need for, and potential of a different mindset and associated inner qualities to support the negotiation and activation of climate
The results from CV measurements demonstrate that the investigated hydrogel biopolymer electrolytes exhibit properties comparable to those of liquid electrolytes, char- acterized
(2004) Microbial sulfate reduction in deep sediments of the southwest Pacific (ODP Leg 181; Sites 1119 to 1125): Evidence from stable sulfur isotopes and pore water modeling..
Thus, the aim of the present study was to evaluate the leaching of residual monomers from pure blocks of the low- viscosity infiltrant compared to the different conventionally
Ehrnsten, Crack Growth Behaviour of Low Alloy Steels for Pressure Boundary Components under Transient Light Water Reactor Operating Conditions (CASTOC), Minutes of the 2004
Table 1 Control variables’ levels, codes, names and brief descriptions for the analysis of knowledge flows* * All variables in Table 1 are treated as scale variables in IBM®
A systematic review of teaching professional- ism in postgraduate medical education also reveals that medical ethics in practice is one of the most common professionalism topics
Abstract: Thematic Conference Advanced Materials Thematic Conferences Advanced Materials The project “Thematic Conferences on Advanced Materials” aimed at supporting the German